通过分析汽车发动机制造企业对刀具管理的信息化需求、SAP及MES刀具管理模块功能的需求,详细阐述了刀具管理系统的构建及应用。刀具管理系统是基于业务流程优化及业务规则而构建,与企业OA、SAP及生产线MES系统集成,并将刀具管理系统应用至车间,实现刀具全生产周期管理、刀具实体ID化管理及刀具寿命管理等。系统上线应用后已取得较好成效。
刀具作为发动机制造加工生产线的重要组成部分,其性能及质量直接影响生产线的加工节拍及生产效率。如何合理管控刀具、降低刀具成本及库存已成为企业需要持续思考的问题。
随着新一代信息技术的不断发展及智能制造的深入应用,传统的人工纸质管理模式已无法满足生产线刀具管理需求[1],仅靠企业资源管理系统SAP及制造执行系统MES进行刀具管理已难以满足现有需求,需利用信息化手段,构建企业级的刀具管理系统,通过系统间的数据集成及应用,挖掘数据价值,提升刀具信息化管理水平,实现企业整体的降本增效。
刀具的生命周期活动从刀具计划开始,直至刀具报废。具体步骤为:计划→采购→公司一级库管理→工厂二级库管理→车间领用→刀具装调→刀具使用加工→判断刀具是否报废或磨损→对可重磨刀具重磨→刀具重用→刀具报废。发动机制造企业中的刀具管理,按业务功能分类可分为刀具主数据管理、刀具流转管理、刀具仓储管理、刀具使用绩效分析及刀具寿命监测。其中,刀具主数据管理包括刀具图样及参数、工艺参数、工单数据、刀具清单、刀具仓库管理等。刀具流转管理包括备刀需求、刀具选择、刀具组装及测量、刀具安装及拆卸、刀具修磨及回收等。刀具仓储管理包括仓库设置、储位设置、出入库管理、安全库存及线边库管理等。刀具使用绩效分析及刀具寿命监测包括刀具消耗、刀具成本分析、换刀异常率及刀具寿命统计等。
刀具管理的信息化,首先要覆盖刀具管理的全部业务,贯穿刀具全生产周期,实现管理的信息化、透明化,以提升作业效率;其次,需完成对刀具库存、使用、成本、呆滞和刃磨等多维度分析,减少浪费;最后,通过刀具的寿命监控、数据建模分析等,从而挖掘数据价值,实现刀具的寿命预测,以延长刀具寿命。
3.1 SAP系统刀具管理
SAP系统刀具管理是当前很多发动机制造企业采用的刀具管理模式,主要基于SAP系统的MM、PM模块,辅以手工录入表格、人工统计方式进行[2]。
SAP系统主要实现了刀具的主数据管理、刀具物料号管理及刀具的采购、公司一级库管理、工厂二级库的保管及出库的消耗、成本结算等管理,但刀具在二级库出账后的车间领用、刀具装调、修磨、报废、刀具重磨上线、拆卸回收及刀具寿命等业务无法在SAP系统进行管控。多数企业在这些环节主要依靠人工管理和人工记录,费时费力,出错的风险系数较高。
3.2 MES系统刀具管理
MES是制造执行系统,通过采集生产相关硬件/软件的各种数据和状态信息,实现企业从生产订单下达到完成产品生产交付活动全过程的监控及管理,重在过程的执行与监控。我公司的机械加工MES系统刀具管理模块主要是通过管控刀具在设备上的使用,与当前订单关联,实现对应的报表统计,具体功能如下。
(1)装刀操作人员在装刀时,将刀具RFID对准设备上刀位配套的RFID读写头,读取RFID内刀具的几何尺寸以及刀具寿命值,并写入设备对应的PLC。
(2)卸刀操作人员在刀具管理画面中选择要卸载的刀具,将刀具从刀库中取出,放到RFID读取位置的刀架中进行卸载确认操作,同时此操作将刀具的信息(含刀具剩余寿命等信息)写入刀具的RFID芯片中。
(3)刀具实时监控及寿命报警可显示刀具的实际数据,如基本刀具数据、每把刀具的寿命数据以及刀具的位置信息,并根据寿命设置触发换刀提醒,通过企业微信或终端向相关人员推送。
(4)刀具使用查询刀具与当前设备、加工工件ID及订单绑定,可根据刀具ID快速查询到刀具信息,如刀具正在哪台设备使用、刀具参数、寿命等数据,使用次数、加工时主轴负载、加工的工件编号等信息。
从以上分析可看到,MES对刀具的管理主要体现在刀具的上线使用、刀具的拆卸使用、当前刀具的寿命监控及报警中,重在使用过程的监控及管理,对刀具的备刀装调管理、刀具修磨及报废、绩效分析等仍需线下人工记录及管理。
3.3 SAP/MES刀具管理存在的问题
通过SAP及MES,基本满足了刀具计划→采购→公司一级库管理→工厂二级库管理、刀具加工的信息化需求,但刀具从工厂二级库领用后,刀具装调、刀具修磨及刀具重用就会失去系统管理,致使刀具管理没有覆盖全业务流程。由于中间环节没有系统监控,部分刀具闲置而不知,易造成重复采购的问题;刀具管理没有实现刀具实物ID化,无法记录重磨、重调后的刀具检测数据,不便于进行刀具寿命和成本分析,无法精准核算成本,存在绩效分析困难的问题。SAP及MES均不适合管理刀具图样及刀具的BOM管理,无图样版本管理查阅不便。总的来说,仅用SAP及MES的刀具管理仍存在管理不透明、数据一致性差、刀具闲置浪费及管理效率低等问题,无法做到成本最小化、效率最大化。
根据需求及现状,从业务改善及未来拓展出发,制定刀具信息系统的技术路线为:梳理原业务痛点→优化刀具管理流程→制定刀具业务规范→构建刀具信息化系统→系统试用及功能优化。
4.1 优化刀具管理流程
针对刀具业务现状,对刀具全流程业务数据流进行梳理,可看出刀具数据流的断点主要集中在刀具从二级刀库到车间的领用、装调、修磨及报废环节。为实现系统数据贯通,现新增车间刀库,用来管理MES生产计划用刀的出入库及操作人员领用情况,并将现场的组刀、装刀、拆刀、修磨刀及报废归入备刀室管理[3]。调整后,除刀具在设备上外,其他环节均有对应刀库管理,优化后业务流程如图1所示。
图1 优化后业务流程
刀具的实物流为:SAP公司一级刀库→SAP工厂二级刀库→备刀库→车间刀库→领用→上刀到设备机台→下刀归还车间刀库→备刀室,进行拆刀后的归还、修磨、换刃或刀具报废处理。
刀具业务信息流为:备刀室依据生产任务生成备刀任务→备刀任务拉动刀具/刀柄/附件从二级库或一级库的领用和装调刀→完成组合刀组装,相关信息写入RFID,入库到车间刀库,生成组装记录、组装刀入库和库存记录→刀具领用,上刀,刀具信息RFID读取并写入设备→加工完成,下刀,刀具使用信息写入RFID→刀具归还车间刀库→备刀室拆刀处理。
4.2 制定刀具业务规范
根据业务及未来拓展需求,对刀具业务及其数据重新约束及规范化。
(1)刀具实体ID化管理 刀具唯一码管理即刀具或组合刀在使用前需制定实体的唯一编号,以利于识别及管理。刀具实体ID化管理主要面对非耗材类刀具。此类刀具在SAP上有图号、物料号,但没有刀具实物的唯一码,不利于刀具的实物管理及数据分析。目前行业内多使用刀具种类、物料号及流水号的组合方式作为刀具的唯一码,但该码的位数往往大于8位,超出实际生产设备所用FANUC系统的字段限制。为此,制定刀具的唯一码规则为:单体刀具,可直接用刀具编号作为刀具的唯一码;组合刀具,其刀柄或刀盘、刀片及辅具均有对应编号,组合后可使用刀柄或刀盘的唯一编号作为刀具的唯一码,后续可通过系统关联方式管理该刀柄对应的刀片及辅具,采用按2位年代号+6位流水码作为刀具实物的唯一码,满足设备数控系统限制,刀具的种类、物料号、图号等其他信息通过系统集成方式进行关联使用。已印刻ID的刀具实体如图2所示。
图2 已印刻ID的刀具实体
(2)规范组合刀的寿命计算规则 寿命计算到单刀,并记录拆刀归库的剩余寿命,以备下次使用。由于公司产品加工的特殊性,刀具寿命以加工指定产品的特定工序的次数计算。
1)组合刀寿命。组合刀需根据对应加工零件种类、材质差异计算其寿命,并取其单刀寿命的最小值。组合刀在加工不同材料零件时,其寿命也不同,如某刀具的基准寿命是1000次,但在某工序中因材质、工艺等原因仅能使用800次,则设定寿命系数为0.8。组合刀由多个单刀组成,每个单刀的寿命不同,组合刀寿命取其单刀寿命的最小值。如组合刀A由单刀1、单刀2组成,组刀前单刀1、单刀2的剩余寿命分别是1000次、800次,寿命系数为0.8、0.6。组刀后,单刀1、单刀2在当前工序的剩余寿命计算如下:单刀1组合刀寿命=1000×0.8=800(次),单刀2组合刀寿命=800×0.6=480(次),则组合刀A的寿命取最小值,即单刀2的寿命值为480次。
2)用刀剩余寿命。组合刀在同一设备同时加工不同的产品,因产品的结构差异,故刀具使用的次数也不同。根据产品差异,设定刀具的产品系数。组合刀的用刀剩余寿命=组合刀寿命-加工件数×产品系数。
如上述组合刀A的基准寿命是以加工四缸缸盖测算的,但在同工序加工六缸缸盖时,加工件数是加工四缸缸盖的一半时就需要换刀,设定其加工六缸缸盖的产品系数为2。当前工序已加工了30件六缸缸盖,则组合刀A的用刀剩余寿命=480-30×2=420(次)。
3)单刀剩余寿命。拆刀后,各单刀的剩余寿命要按寿命系数及产品系数对应还原,以备下次使用,单刀剩余寿命=(单刀组合刀寿命-工序加工次数×产品系数)/寿命系数。
如上所述,组合刀A在当前工序加工了30件六缸缸盖后下刀、拆刀,单刀1的剩余寿命=(800-30×2)/0.8=925(次),单刀2的剩余寿命=(480-30×2)/0.6=700(次)。
(3)设立车间刀库 此库可为虚拟库,或作为新购刀柜做实物管理,管理MES生产计划用刀的出入库及操作人员领用情况,将现场的组刀、拆刀、修磨刀及报废归入备刀室管理系统。根据车间刀库情况,结合生产线MES系统,实现现场每一把刀具的位置清晰、可追踪,彻底解决了原刀具领用后具体位置不明的问题,同时为车间刀具的库存、刀具使用率统计、库存资金统计及成本分析奠定了精细化基础。
(4)建立刀具三个维度的成本分析方式 第一,从财务角度计算传统的刀具成本(刀具消耗金额/产量);第二,通过工艺BOM关联工序与背吃刀量、四缸/六缸按不同比例分摊成本的原则,解决了工艺和刀具使用量难以关联、四六缸共线加工刀具成本无法科学分摊的问题;第三,对长寿命刀具,利用刀具ID计算到单把刀具的成本,可对比同一规格的刀具不同个体之间的成本差异。
(5)重新制定刀具采购需求规则 增加已采购尚在途的刀具因素,减少由于已在途信息不透明造成的采购重复浪费,即系统对低于最小库存数量的刀具自动生成采购需求清单,采购需求数量=安全库存→车间刀库库存→SAP车间二级库库存→SAP工厂一级库库存→SAP在途刀具数据。
4.3 系统网络架构及集成
刀具管理系统基于B/S网络架构设计,部署在云端的服务器,服务器资源需要包含了数据库服务器和应用服务器。数控机床通过数据协议实现刀具寿命的采集。车间现场通过智能终端实现对机床数据的采集,刀具系统通过数据接口与外部信息系统进行数据交互对接。通过车间和办公室网络实现与车间现场的终端、PC、PDA及看板的交互。
刀具系统从SAP、MES系统同步基础信息、生产计划信息,从而进行刀具全生命周期的管理。通过设备数据采集统计刀具的寿命,向OA系统、企业微信推送修磨、报废、试用审批及换刀提醒信息,集成方案如图3所示。
图3 系统集成方案
4.4 系统功能
根据以上构建刀具管理系统,系统主要功能如下所述,系统界面如图4所示。
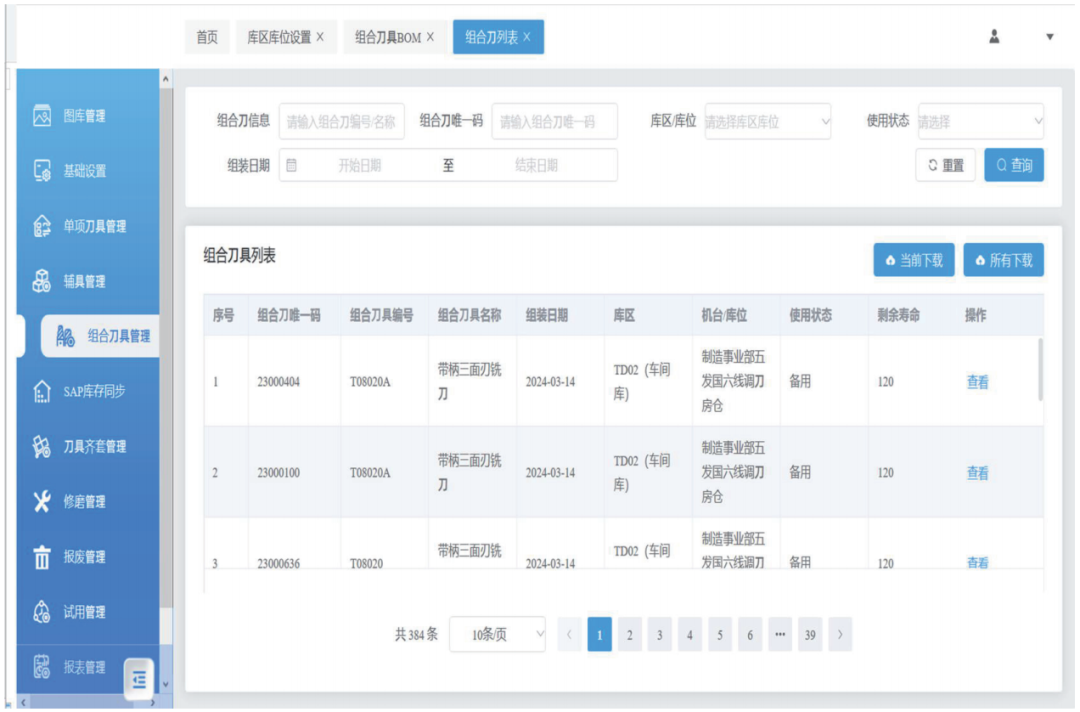
(1)工厂建模包含组织架构,绑定车间与生产线关系,确保生产计划下发时可准确关联至车间,做好产品列表、工序列表、设备列表及刀具清单的设置,维护产品对应工序下的刀具清单,维护每道工序所需的刀具。
(2)刀具主数据管理包括刀具刀柄辅具档案、组合刀档案等。
(3)刀具库存管理具体实现出库单管理、刀具入库管理、刀具出库管理、PDA刀具移库管理、刀具库存台账管理和采购需求管理等。
(4)刀具装拆管理获取MES系统当前的生产计划信息来进行备刀任务管理。依据生产任务中对应产品的刀具清单,计算出需要准备的刀具品种和数量的净需求,结合当前刀具系统中已有的刀具数据,计算出建议组刀的数量,生产管理人员可以通过确认备刀数据下达组刀任务。组刀任务的执行内容包括:扫描或输入刀具、刀柄及辅具的物料信息以完成组刀任务执行,通过换刀/换刃、拆刀任务管理来建立相关信息。
(5)刀具使用跟踪管理及看板管理集成MES获取或使用PDA实现刀具上刀、下刀和换刀操作;增加生产现场的大屏滚动展示刀具的寿命监控信息,对需要更换的刀具进行可视化提醒。
(6)刀具修磨管理实现修磨计划管理、修磨任务管理和修磨数据管理等。
(7)刀具报废管理对拟报废的刀具执行报废操作,具体可分为长寿命刀具和短寿命刀具的报废。
(8)刀具试用管理可以发起刀具的试用流程,审批通过后,进行刀具试用操作并记录和上传试用的报工信息,审批通过后标记试用完成。
(9)绩效分析可从成本、刀具物料号、时间段和工序几方面进行刀具领用的统计分析,按时间段展示单台零件的刀具成本和每工时刀具成本趋势图。对各刀具进行使用率分析,甄别刀具闲置情况,同时进行换刀原因分析、刀具寿命统计分析、调刀人员及磨刀人员的绩效分析等。
该系统投入使用后,将实现刀具核心业务主流程IT化,车间刀具管理无纸化,刀具全生命周期管理透明化、智能化。通过刀具实体ID化管理,可实现刀具(特别是贵重刀具)的全生命周期个体化管理,解决了原批量化管理存在粗糙、不够精准的问题,并使刀具全生命周期管理真正落到具体刀具上。通过加强车间内刀具库的管理及业务流程优化,实现刀具的流转位置追踪、精准的刀具寿命管理、刀具车间库存评价及成本多维度分析等,在发动机制造行业的刀具信息化管理方面取得了较大突破。
本文阐述的刀具管理系统是在优化了业务流程、制定业务规范后构建的智能刀具管理系统,该系统与业务的契合度较高,发挥了软件系统的优势,深入挖掘数据价值,提升了业务水平。实施后,刀具作业效率及成本控制均有较好提升,其中刀具成本降低10%以上,同时减少了10%刀具库存资金,达到了较理想的效果。